
5S on parannustyökalu kurinalaisen ja tuottavan työpaikan järjestämiseen ja ylläpitämiseen. Se auttaa luomaan paremman työympäristön, vähentää hukkaa ja parantaa samalla tehokkuutta, turvallisuutta ja laatua. 5S edustaa viittä yksinkertaista käytäntöä, jotka alkavat S-kirjaimella. Sitä sovelletaan yleisesti tuotantolaitoksissa tuotantolinjoilla, varastoissa, huoltoalueilla ja toimistotiloissa. Nyt sitä sovelletaan yhä useammin monilla eri aloilla, kuten terveydenhuollossa, koulutuksessa, majoitus- ja ravitsemisalalla ja vähittäiskaupassa.
5S on japanilainen johtamismenetelmä, jonka Toyota kehitti alun perin osana Lean Manufacturing -järjestelmää. Se on tärkeä osa lean-tuotantojärjestelmää ja edellytys muiden lean-tekniikoiden, kuten TPM:n ja Kaizenin, edistämiselle. Monet yritykset aloittavat Lean-muutosmatkansa 5S:llä, koska se on yksi helpoimmista Lean-tekniikoista ja paljastaa joitakin näkyvimpiä esimerkkejä hukasta. Monet Lean-asiantuntijat uskovat, että 5S:n avulla on onnistuttava, jotta muiden Lean-tekniikoiden kanssa ei tarvitse kamppailla Lean-toteutuksen aikana.
5S on jäsennelty tapa luoda ja ylläpitää järjestäytynyttä, puhdasta, turvallista ja suorituskykyistä työympäristöä. Kyse ei ole vain ulkonäöstä ja paikan siistinä pitämisestä, eikä se ole myöskään siivoustekniikka. Se on pikemminkin tapa poistaa hukkaa, tunnistaa parannusmahdollisuuksia ja tehdä työpaikasta tehokkaampi ja tuottavampi. 5S auttaa tekemään jätteet näkyviksi kaikille, jotta ne voidaan poistaa heti. 5S:n avulla voidaan eliminoida tai vähentää ylimääräistä varastoa, hukkaan heitettyä liikettä, odottelua etsittäessä tarvittavia tuotteita ja sitä, että osia on enemmän kuin tarvitaan.
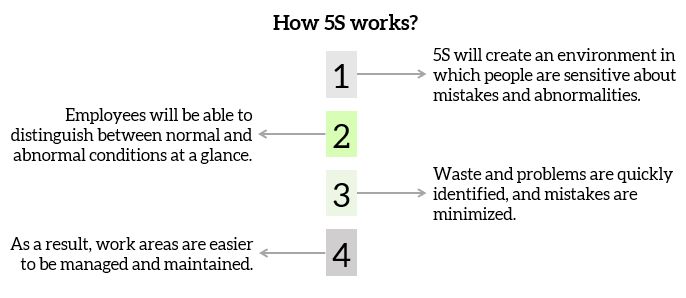
5S:n avulla voidaan eliminoida tai vähentää hukkaa (eli mudaa)
Kaikki tykkäävät työskennellä siistissä ja hyvin järjestetyssä ympäristössä. Kun 5S on otettu täysimääräisesti käyttöön, se voi tehdä työtiloista puhtaampia, turvallisempia ja miellyttävämpiä työskennellä. Puhdas ja siisti työpaikka johtaa siihen, että turha ajanhukka asioiden etsimiseen vähenee ja siten turhautuminen vähenee. Tämä ei ainoastaan helpota kaikkien työtä, vaan saa myös työntekijät tuntemaan olonsa paremmaksi työpaikallaan ja luo työpaikan omistajuutta ja motivaatiota. Se edistää tehokkuutta, kannustaa tiimityöskentelyyn, kasvattaa ylpeyttä ja muodostaa loistavan lähtökohdan muiden Lean-tekniikoiden toteuttamiselle.
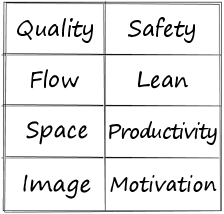
Puhdas ja siisti työpaikka on myös välttämätön tehokkaalle toiminnalle ja sujuvan työskentelyn luomiselle. 5S luo ympäristön, jossa ihmiset suhtautuvat herkästi virheisiin ja epäkohtiin. Työntekijät pystyvät erottamaan normaalit ja epänormaalit olosuhteet yhdellä silmäyksellä. Tämän seurauksena ongelmat havaitaan nopeasti, onnettomuudet ja virheet minimoidaan ja työalueet ovat helpommin hallittavissa. 5S luo myönteisen vaikutelman myös asiakkaisiin, sillä työpaikalla esitettyjen standardien odotetaan heijastuvan toimitettuihin tuotteisiin ja palveluihin. Tämä lisää asiakkaiden luottamusta tuotemerkkiin, parantaa yrityksen imagoa ja tekee siitä kannattavamman ja kilpailukykyisemmän markkinoilla.
5S:ää pidetään joskus erillisenä ohjelmana, joka tarvitsee taloudellisia perusteita. Yksi tärkeimmistä ongelmista 5S:ää toteutettaessa on se, että kustannussäästöjä ei yleensä voida kirjata useimpiin kustannuslaskentajärjestelmiin. Pehmeitä säästöjä syntyy laadun, turvallisuuden ja moraalin osalta, mutta kovia säästöjä, joita voidaan mitata ja seurata, ei synny. Yksi tapa perustella 5S:n arvo on mitata jätteen vähenemistä. Voit esimerkiksi mitata aikaa, joka kuluu työkalujen etsimiseen, tai aikaa, joka kuluu tilan tyhjentämiseen työskentelyä varten. Varmista, että nämä parannukset dokumentoidaan ja että niitä tuetaan tiedoilla ja analyyseillä, sillä näin rakennat perusteluja investoinneille.
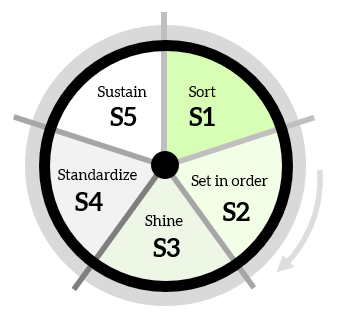
Termi 5S on lyhenne viidestä japanilaisesta sanasta: seiri, seiton, seisou, seiketsu ja shitsuke. Nämä viisi sanaa käännetään englanniksi usein seuraavasti: sorting, setting in order, shining, standardizing ja sustaining. Muutkin englanninkieliset käännökset ovat mahdollisia.
Lajittelu on 5S:n ensimmäinen vaihe. Sillä tarkoitetaan käytäntöä, jossa käydään läpi kaikki työpaikalla olevat tavarat ja säilytetään vain se, mitä todella tarvitaan. Tarpeet ylittävät esineet tulisi joko varastoida muualle tai hävittää. Lajittelun pääajatuksena on tyhjentää alue häiriötekijöistä, jotta voidaan keskittyä siihen, mitä työpaikalle jää. Näin saadaan aikaan vähemmän sotkua ja ajanhukkaa, vapautetaan tilaa ja luodaan virtaviivaisempi työpaikka.
Joitakin lajittelussa käytettäviä strategioita ovat:
- Tarkastetaan kaikki työpaikalla olevat esineet ja määritellään sitten, mikä on tarpeen työn suorittamiseksi. Pidä vain se, mitä tarvitaan, ja poista kaikki muu.
- Poista käyttökelvottomat, rikkinäiset, vanhentuneet, tarpeettomat tai satunnaisesti käytetyt esineet.
- Määrittele standardit tarpeettomien esineiden poistamiselle ja jätteiden hävittämiselle.
- Älä unohda tietokonetiedostoja ja sähköposteja. Arkistoi tai poista tiedostot, joita ei enää tarvita.

Mitä kannattaa poistaa?
Erittäin yleinen lajitteluvaiheessa käytetty työkalu on Red Tag -tekniikka. Se on merkintätyökalu, jota käytetään korostamaan sitä, mikä on tarpeellista tietyllä alueella. Tarkoituksena on selvittää, onko jokin tuote jonkun mielestä tarpeellinen ja missä määrin. Esineet merkitään punaisella merkillä rajoitetuksi ajaksi, jonka aikana niiden käyttöä arvioidaan. Yhden tai kahden viikon kuluttua esineet, joita ei käytetä tai jotka on vedetty pois alueelta, olisi siirrettävä muualle tai niistä olisi päästävä eroon, jolloin työpaikasta tulisi vähemmän häiritsevä.
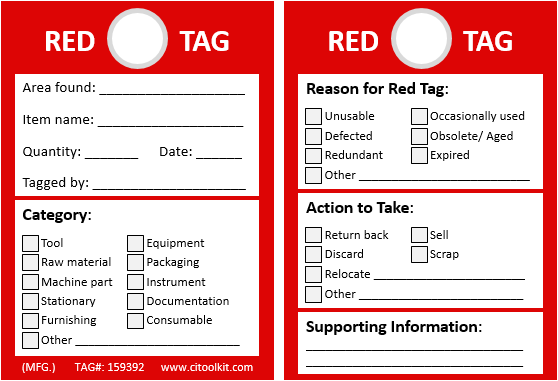
Punainen lappu on merkintäväline, jota käytetään 5S-ohjelman lajitteluvaiheessa
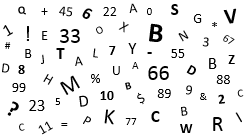
Orjestykseen laittamisella tarkoitetaan käytäntöä, jossa tarvittavat esineet ja tavarat järjestetään niin, että kuka tahansa löytää ne helposti ja pääsee niihin käsiksi. Siinä määritellään, missä ja miten työn suorittamiseen tarvittavat esineet on järjestettävä. Kun olet poistanut kaikki tarpeettomat esineet, palaa jäljelle jääneisiin esineisiin ja järjestä ne niin, että tarvittavat esineet on helppo löytää. Sen pitäisi näkyä yhdellä silmäyksellä, jos jokin esine ei ole sille osoitetulla paikalla. Tämä parantaa työnkulkua ja vähentää hukkaan heitettyä aikaa ja liikettä.
Joitakin tässä vaiheessa käytettäviä strategioita ovat:
- Vaihda suljetusta varastointijärjestelmästä avoimeen varastointijärjestelmään.
- Kohdista paikat kaikille laitteille, työkaluille, varaosille ja materiaaleille.
- Organisoi esineet modulaarisiin kaappeihin, säilytyslaatikoihin, vetolaatikoihin, hyllyihin ja telineisiin.
- Käytä värien mukaista värikoodausta, jolla voit kohdistaa työkalut eri osastoille.
- Kirjoita kaapit, säilytyslaatikot, hyllyt ja telineet.
- Kirjoita ja merkitse varastointialueet, pinoamisalueet ja turvalaitteiden paikat.
- Merkitse minimi- ja maksimitasot selkeästi, jotta näet yhdellä silmäyksellä, kuinka monta varastotavaraa on jäljellä.
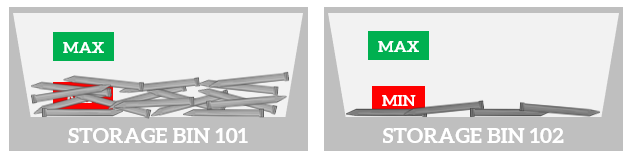
Merkitse minimi- ja maksimitasot selkeästi
Seuraavaksi tulee kiillotusvaihe. Shiningin tavoitteena on luoda puhdas työpaikka, jossa ei ole roskia, likaa tai pölyä. Tämä mahdollistaa poikkeavuuksien, kuten toistuvan saastumisen ja öljyvuotojen, helpon tunnistamisen ennen ongelman pahenemista. Kiillotus auttaa myös luomaan omistajuutta työalueeseen, mikä tekee siitä turvallisemman ja miellyttävämmän työskennellä.
Joitakin kiillotuksessa käytettäviä strategioita ovat:
- Katoaa kaikenlainen lika, kontaminaatio ja epäjärjestys.
- Puhdista, pölytä, kiillota ja lakaise huolellisesti.
- Puhdista kaikki työkalut ja laitteet.
- Tunnista ja poista likaantumisen syyt.
- Tunnista jätteiden säilytystilat ja puhdista ne säännöllisesti.
- Valmistele työvuoroluettelo ja jaa vastuualueet.
- Älä unohda tietokoneita, kalusteita, kaappeja, säilytysastioita, työpisteitä ja näyttötauluja.
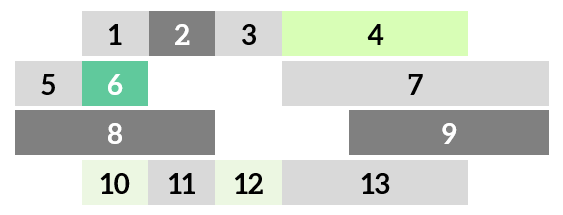
Jaa työpaikka vyöhykkeisiin ja jaa henkilöt, jotka vastaavat kustakin vyöhykkeestä
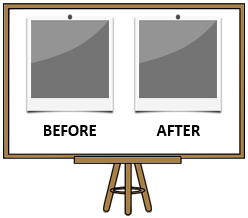
Työpisteen siisteydestä ja järjestyksestä huolehtiminen on todellinen haaste, ja se onnistuu vain, jos laaditaan standardit ja niitä noudatetaan. Standardointi tarkoittaa sitä, että tehdään oikeat asiat aina oikein. Se on standardien ja odotusten kommunikointia ja ylläpitoa koko työpaikalla. Kun opit lisää, päivitä ja muokkaa standardejasi, jotta 5S-käytännöistä tulee yksinkertaisempia ja helpompia.
Joitakin standardoinnissa käytettäviä strategioita ovat:
- Valmistele menettelyt ja aikataulut, joilla varmistetaan kolmen ensimmäisen S-käytännön toteuttamisen johdonmukaisuus.
- Suunnittele työskentelyrakenteet, jotka tukevat uusia toimintatapoja.
- Varmistu siitä, että kaikki tietävät, mikä on heidän vastuualueensa, jotka liittyvät lajittelun, järjestelyn ja siivouksen suorittamiseen.
- Käytä valokuvia ja visuaalisia kontrolleja, jotka auttavat pitämään kaiken sellaisena kuin sen pitäisi olla.
- Katsele 5S:n toteutuksen tilaa säännöllisesti auditointitarkastuslistojen avulla.
- Käytä koneiden puhdistuksen/voitelun tarkistuslistoja.
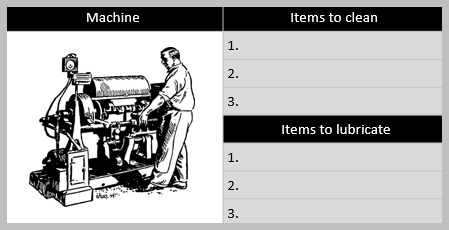
Koneiden puhdistuksen/voitelun tarkistuslomakkeet
Kun neljä ensimmäistä vaihetta on toteutettu, on nyt keskityttävä saavutetun ylläpitämiseen. Ylläpito on neljän ensimmäisen S-käytännön kurinalaista soveltamista, jotta 5S-ohjelma olisi menestyksekäs. Se on ylivoimaisesti vaikeinta toteuttaa. Monet yritykset ovat huomanneet, että niiden likaiset tilat ovat sekaisin sen jälkeen, kun ne ovat yrittäneet toteuttaa 5S:ää.
5S:llä on taipumus epäonnistua, kun ylhäältä puuttuu omistajuus ja kun johto ei kiinnitä siihen jatkuvaa huomiota. Johtajien on ostettava mukaan ja sitouduttava henkilökohtaisesti ohjelmien onnistumisen varmistamiseksi. Heidän on luotava kulttuuri, jossa odotetaan 5S:n huippuosaamista eikä vähempää suvaita. Ohjelman menestyksekäs jatkuminen edellyttää asianmukaista suunnittelua, koulutusta, seurantaa ja virallista tilivelvollisuusjärjestelmää.
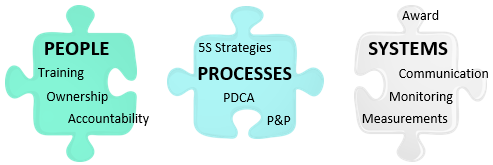
Kannattavuus on ihmisten, prosessien ja järjestelmien tehokasta vuorovaikutusta
Joitakin strategioita, joita on toteutettu saavutettujen hyötyjen ylläpitämiseksi, ovat muun muassa:
- Käyttäkää 5S-julisteita ja kylttejä muistuttamaan hyödyistä.
- Varmistakaa, että kaikki ovat osallisina toiminnassa ja että kaikki ovat siitä vastuussa.
- Tee siitä osa työterveyttä ja -turvallisuutta.
- Tee siitä osa päivittäistä Gemba-kokousta.
- Varmista, että kaikkia määriteltyjä standardeja noudatetaan.
- Kommunikoi auditoinnin tuloksista.
- Varmista tuloksia asianmukaisten mittareiden ja analyysien avulla.
- Palkitse ja tunnusta ponnistelut ja saavutukset.
Miten 5S otetaan käyttöön
Paras lähestymistapa on aloittaa pilottityöalueesta ja käyttää sitä mallina muulle yritykselle. Aloita siitä, mikä on yksinkertaisin, tai etsi ongelma, jonka ratkaisemisessa 5S:llä on keskeinen rooli.
Seuraavissa vaiheissa kuvataan, miten 5S otetaan käyttöön yhdellä alueella:
- perusta 5S-tiimi ja nimitä tiiminvetäjä kyseiselle alueelle.
- Havainnoi aluetta ja arvioi nykytilanne.
- Kerää tietoja ja ota “ennen”-valokuvia.
- Aivoriihi tiimin kanssa parannusmahdollisuuksien kartoittamiseksi.
- Valmistetaan parannussuunnitelma, jossa eritellään yksityiskohtaisesti toiminnot, vastuualueet ja aikataulut.
- Toteutetaan suunnitelma alueen parantamiseksi. Käytä riittävästi aikaa kuhunkin S-kohtaan.
- Auditoi alue ja ota jälkikuvia.
- Kehitä ja toteuta valvontasuunnitelma parannuksen ylläpitämiseksi.
- Kun olet luonut hyvän esimerkin ja osoittanut onnistumisen, voit luoda suunnitelman, jolla edetään alue kerrallaan.
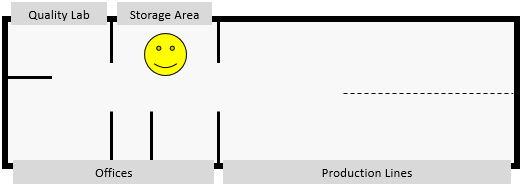
Ohjelman etenemistä ja vaikuttavuutta tulisi arvioida säännöllisesti. Tämä voidaan toteuttaa 5S-auditoinnin tarkistuslistan avulla, joka auttaa varmistamaan, että 5S-standardit täyttyvät. Se antaa tarkkailijalle mahdollisuuden puuttua paremmin vaatimustenmukaisuuden puutteisiin ja tarjoaa mahdollisuuden jatkuvaan parantamiseen. On tärkeää, että myös ylin johto ja esimiehet osallistuvat näihin tarkastuksiin. Tehokkaan auditoinnin pitäisi päätyä myös luetteloon parannustoimista.
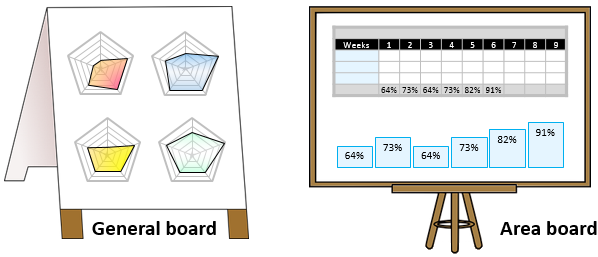
Auditoinnin tuloksia voidaan jakaa tiedotustaulujen avulla
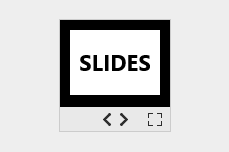
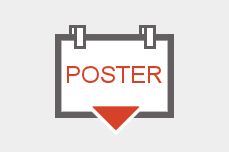
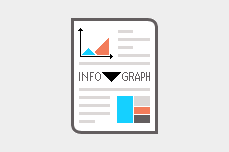
avulla
.